The key to our system is a centering bar which consists of two wear resistant spheres fastened at opposite ends of a flat spring steel bar. These act as lubrication free bearings, minimising wear on the aluminium and brass tracks in which the mechanism constantly moves. The bars are positioned diagonally across the joint opening. The spring steel centering bar holds the cover plate central and the fixing screws tight.
When you select Latham Self Aligning Flexible Mechanical Expansion Joint Covers, and have a special configuration fabricated, you are taking advantage of a unique solution to the problem of keeping joint covers firmly anchored despite movement between sections of concrete flooring. This ensures a long-lasting, trouble free and stable floor base.
The mechanical expansion joint covers are designed to permit multi-directional six-way movement. The cover unit is free to move horizontally, vertically, and horizontally in shear without damaging the surrounding concrete and paving, deforming the cover plate or shearing the screws holding the cover plate in place. Whatever your project, Latham Flexible Mechanical Expansion Joint Covers are available and can be fabricated to almost any width or required joint movement. Optional water gutters or fire barriers are part of the totally trouble free full joint system.
All Latham Mechanical Expansion Joint Covers unless otherwise detailed are designed for normal pedestrian applications. If the application is heavier e.g. high traffic areas like railway stations or airports or where heavier loads may transverse the joint cover, see the heavy duty and vehicular ranges, consult Latham Australia to specify a suitable cover thickness.
All Latham Expansion Joint Covers offer various amounts of movement as indicated by the symbols associated with systems and the related tables detailed below. All systems will accommodate general thermal expansion and contraction and shrinkage as indicated. In some cases depending on the requirements of the structure, standard systems also will allow seismic movement, although in applications where a structure has been designed to accommodate extreme seismic movement the Latham Seismic Range of expansion joint covers should be considered.
Materials
Metals
Extrusions used in Latham Expansion Joint Covers are aluminium 6063-T5 & T6 mill finish alloy, brass 380 mill finish alloy or stainless steel decks, Type 304 Grade, 2B finish to 3mm thick, thicker stainless steel decks are supplied in No.1 finish. On request other stainless steel finishes are available if specified at time of order and subject to minimum order quantites. When expansion joint covers are being installed in areas of high temperature change or in continuous runs, special consideration should be given to thermal expansion of the metal components, which is approximately 0.025mm per metre, per degree Celsius of temperature change. Allowances should be made accordingly for side members and particularly cover plates during installation.
Vinyl
All vinyl plastic extrusions used are polyvinyl chloride (thermoplastic). This material has extreme versatility; it is light weight, strong, tough and inert to most chemicals. It is a metallic grey colour in most profiles, blending with our standard finishes. Other colours may be available for large volume orders or as detailed on the specific product page in this catalogue. Some expansion joint inserts are supplied with neoprene or santoprene inserts.
Finishes
Coatings
Titazel PE31, is a protective coating applied to all steel members to protect and control electrolytic action. Clear Anodised 20 micron finish is standard for all wall and ceiling visually exposed cover units, with the exception of the M, ML, MSM and MLSM Series which are supplied mill finish unless otherwise specified.
Protective Tape
All exposed anodised aluminium surfaces will be supplied covered with protective film/tape to be removed on application. Materials covered with protective tape should not be subjected to prolonged sunlight or extreme temperatures and the tape should be removed within 30 days of delivery.
Materials
Cover Plates
All aluminium, brass and stainless steel floor cover plates are discretely stamped on the surface close to one end as manufactured by Latham Australia, which ensures installed material can be identified in the future and is the clients confirmation that the specified product has been installed. Cover plate thicknesses may vary for aluminium and stainless steel. Confirm cover plate thickness with the technical sheet for the selected profile, available from Latham Australia. Thicker, wider cover plates may protrude slightly above the side member, but are supplied with a half height bevel at 45° on most covers.
Standard Product Lengths
All material is supplied standard in the following full lengths: Aluminium Standard and Heavy Duty Series – 3050mm, Aluminium Light Duty Series – 4000mm, Brass – 4000mm, Stainless Steel Decks – 3050mm.
Components
Spring Steel Centering Bars
The spheres attached to the spring steel centering bars act as nylon bearings, minimising wear and tear of the embedded cylindrical channel members. The centering bars are specially treated and produced from specially hardened spring steel. Light tension from the cover plate to the centering bar, through the screw, reduces the likelihood of the screw becoming loose. All Latham spring steel centering bars are treated with Titazel PE-22 coating or Titazel PE-20 zinc coating to assist in protecting the centering bars from moisture etc. Most centering bar screws are supplied to suit a small Phillips head screwdriver to help ensure the system is not over tightened causing the centering bars to lock and possibly snap.
Anchors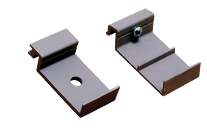
CA-16 aluminium/BM-16 brass block-out or CA-6 aluminium/BS-6 brass cast-in type anchors in standard applications are installed at500mm centres on both sides of the embedded members. CA-16 aluminium/BM-16 brass block-out anchors will be supplied unless otherwise specified. To specify CA-6 aluminium/BS-6 brass cast-in anchors for ranges suited to these angles specify “Latham Mechanical Expansion Joint Cover Type…… with CA-6/BS-6 cast-in anchors”. Latham Australia recommend that all embedded aluminium members be coated with Tnemec PZ9 protective coating (optional extra) - see below.
Fixing Holes and Locations
Most expansion joint covers are supplied with side members pre-drilled to suit fixing sizes as indicated on the relevant joint series page in this publication.
Splices
Where applicable to the joint type specified, CA-16 block-out or CA-6 cast-in splices are supplied to assist with positive alignment of aluminium embedded members. Latham Australia recommend that all embedded aluminium members be coated with Tnemec PZ9 protective coating (optional extra) - see below.
FC2 Form Clips
For cast-in place installations FC2 form clips allow the embedded member with anchor to be set accurately on the form work. These can be supplied when CA-6 cast-in anchors have been specified (optional extra).
Optional Extras
Tnemec PZ9 Protective Coating
A coating applied to aluminium surfaces that are to be embedded in cement, Tnemec PZ9 protective coating should be considered to minimise corrosion and electrolytic reaction with embedded members. Latham Australia recommend the use of Tnemec PZ9 for all embedded sections, particularly externally and in areas where water or moisture is common. Specify “with Tnemec PZ9 Protective Coating”.Slip Resistant Surfaces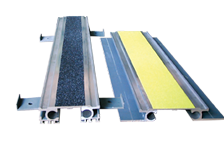
A re-surfaceable slip resistant coating can be applied to most of the aluminium, stainless steel and brass cover plates. Slip resistant coating when specified will be supplied in black colour unless otherwise specified. Other coating colours available. Limited warranty applies. Contact your Latham Australia technical representative. Specify “with re-surfaceable slip resistant coating”.Powder Coating/Anodising
Powder coating or anodising can be applied to all exposed aluminium surfaces. Latham Australia does not recommend powder coating or anodising for floor or floor to wall expansion joint covers, as the surfaces are often easily scratched by foot traffic. Specify type of coating and colour required. Interior/exterior wall and exterior roof joint covers, can be successfully powder coated or anodised to harmonize with the surrounding finishes. Contact your Latham Australia Pty Ltd technical representative for further details.Protective Tape Coating
Available for all mill finish exposed products. Specify “with protective tape coating”. Also see Finishes above.Water Gutter
Available for most Latham expansion joint covers (available with all ranges that carry() symbol in the description), Latham expansion joint water barriers are made of high quality flexible PVC for the VWS Series, and Neoprene for the BFG Series. Water barriers are furnished in continuous lengths where possible to reduce field splicing.
While exterior wall covers effectively keep most water out of the joint, wind, blowing rain and seepage require the use of water barrier at exterior joints. Water barriers are also suggested for interior floors subject to mopping and washing. Specify “V” after the product code for water barrier e.g. CA-25V.At exterior walls, water should drain freely to the exterior at the base of the joint cover. When difficult drain points occur in roof and floor joints, a flexible PVC drain tube may be installed allowing drainage to building drain systems.
Fabricated Metal Sections
Latham Australia recommend that all corners, cross overs and tees, be factory fabricated for effective performance.Cutting to Length and Factory Assembly
All expansion joint ranges can be factory cut from full lengths to site supplied measurements if required, at extra cost. All recessed and surface mounted expansion joint covers can be factory assembled for quicker installation if required. Specify “factory assembled”. Note: some profiles need to be assembled on site.Packing and Bedding Compound
Latham Australia recommend a high strength non shrink grout be used for filling all recesses for standard pedestrian joint covers. Higher strength epoxy grout should be used in special and extreme conditions including all vehicular applications.Mechanical Fixings
Fixings are not supplied by Latham Australia. Suitable fixings for your application should be sourced, ensuring the expansion joint cover is securely fixed to the structural slab at the indicated centres on the relevant page of this publication for the joint cover selected.Latham Australia Fire & Smoke Barriers
Latham Fire & Smoke Barriers should be used with Latham Expansion joint covers to provide systems with 2 and 4 hour fire ratings. Latham Fire & Smoke Barriers can be used with most Latham wall, ceiling and block out type floor expansion joint covers. Latham Australia Fire & Smoke Barriers allow expansion and contraction, vertical shear and limited horizontal shear movement. Contact Latham Australia Pty Ltd for installation criteria. Fire rated wall joint covers are available for gypsum wall board and masonry construction. See Fire Rated Systems on this website.
Note 1: Movement referred to in this publication should be viewed in the following way. The + (positive) factor refers to the effective amount the joint cover can extend (the joint in the slab increases in width), whilst the – (minus) factor refers to the effective amount the joint cover can contract (the joint in the slab decreases in width). These are effective movements, the systems may be effected by load and traffic volume and other circumstances, which may require a larger or heavier system to be considered. All movements shown in the tables refer to the expansion joint cover being in its standard installation configuration A (as detailed in tables). Altering the installation position will alter the available ± movement, but will not alter the total available movement.
Systems also offer vertical movement and horizontal shear as indicated by the relevant symbol associated to the particular joint cover. The amount of this is dependent on the system and the joint width. Consult Latham Australia for further information in relation to a specific joint cover.
Note 2: All specifications, should be written in conjunction with Product Information - Optional Extras and the Architectural Specifications from this website.
Note 3: For confirmation of cover plate thickness for profiles on this website that refer to more than 1 cover plate type, refer to the actual technical drawing relating to the required expansion joint cover. Contact your Latham Australia Pty Ltd technical representative for further details.